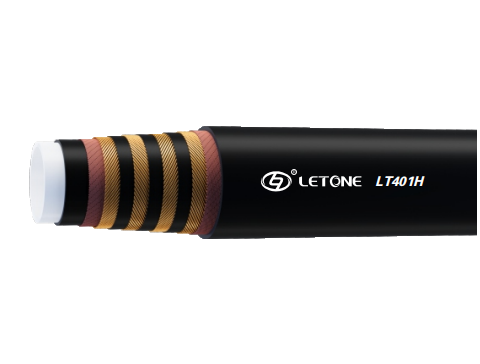
从实验室到生产线:软管工厂的“耐酸基因”解码
在芯片蚀刻液、医药中间体、湿法冶金等领域,酸性介质的输送精度与安全性直接关乎产品良率与人员安全。专注于酸性溶液和化学品的软管工厂,正以“产学研用”一体化模式,将实验室的耐酸材料转化为工业现场的“确定性方案”。
产学研融合:从“分子设计”到“工业验证”
软管工厂与高校、科研院所的协同创新已成常态:
材料联合研发:某工厂与中科院联合开发“含硼氟橡胶”,通过引入硼原子形成三维交联网络,使软管在氢氟酸中的溶胀率从8%降至0.3%,性能达国际领先水平。
失效分析实验室:建立“材料-结构-工况”三维数据库,某电池企业通过该平台快速定位软管腐蚀原因,将新品开发周期缩短60%。
行业标准制定:主导起草《耐强酸软管技术规范》,,推动行业从“经验驱动”转向“数据驱动”。
客户共创:从“产品交付”到“解决方案”
软管工厂正以“场景化思维”重构服务模式:
定制化设计:某光伏企业因现有软管无法耐受氢氟酸+硝酸混合液腐蚀,工厂通过CFD模拟优化流道结构,使软管寿命从1个月延长至18个月。
驻场技术支持:在某半导体工厂酸洗产线升级中,工程师团队驻场3个月,完成从管道布局到软管选型的全流程优化,将酸液泄漏风险降低95%。
备件即服务(MaaS):推出“耐酸软管订阅制”,按使用时长或流量计费,某化工集团通过该模式节省30%的库存成本。
绿色转型:从“耐酸性能”到“循环经济”
软管工厂的可持续创新体现在全产业链:
生物基原料替代:采用玉米淀粉发酵制得的1,4-丁二醇(BDO)合成耐酸聚氨酯,使软管生物基含量达40%,碳排放降低35%。
再生材料利用:开发“废旧软管回收-裂解-再聚合”技术,某工厂通过该工艺将再生氟橡胶含量提升至25%,性能衰减率低于5%。
零废弃生产:通过3D打印技术制造软管模具,减少材料浪费;采用水性胶粘剂替代溶剂型胶水,VOCs排放降低90%。
未来展望:智能软管与量子工业的“技术前哨”
软管工厂的前沿探索已触及未来工业:
自感知软管:集成压电传感器的“智能软管”可实时监测酸液流量、温度与腐蚀速率,数据通过5G网络传输至控制中心,实现预测性维护。
量子计算优化:利用量子算法模拟酸液分子与软管材料的相互作用,某实验室通过该技术将新型耐酸材料的研发周期从5年缩短至18个月。
当耐酸软管工厂从“产品制造商”升级为“解决方案提供商”,其背后是材料科学、智能制造与循环经济的深度融合。从实验室的分子结构到生产线的酸性洪流,这场“耐酸基因”的解码之旅,本质是为工业文明锻造“可弯曲的确定性”——在守护安全与效率的同时,也为人类应对极端环境挑战提供隐形支撑。
留言表单
需求
请填写您的姓名和留言,如果您愿意,请不要忘记邮件和/或电话。我们将在 24 小时内回复。